When it comes to constructing or renovating a building, selecting the right materials is crucial. Among these materials, laminated veneer lumber (LVL) beams have gained popularity for their strength, versatility, and sustainability. This article aims to guide you through the process of choosing the right LVL beam for your structural needs, ensuring that your project is both safe and efficient.
Understanding LVL Beams
Laminated veneer lumber (LVL) beams are engineered wood products made from thin layers of wood veneer that are glued together. This process creates a strong and stable beam that can be used in various structural applications. Unlike traditional timber, LVL beams are manufactured to precise specifications, making them a reliable choice for builders and architects alike.
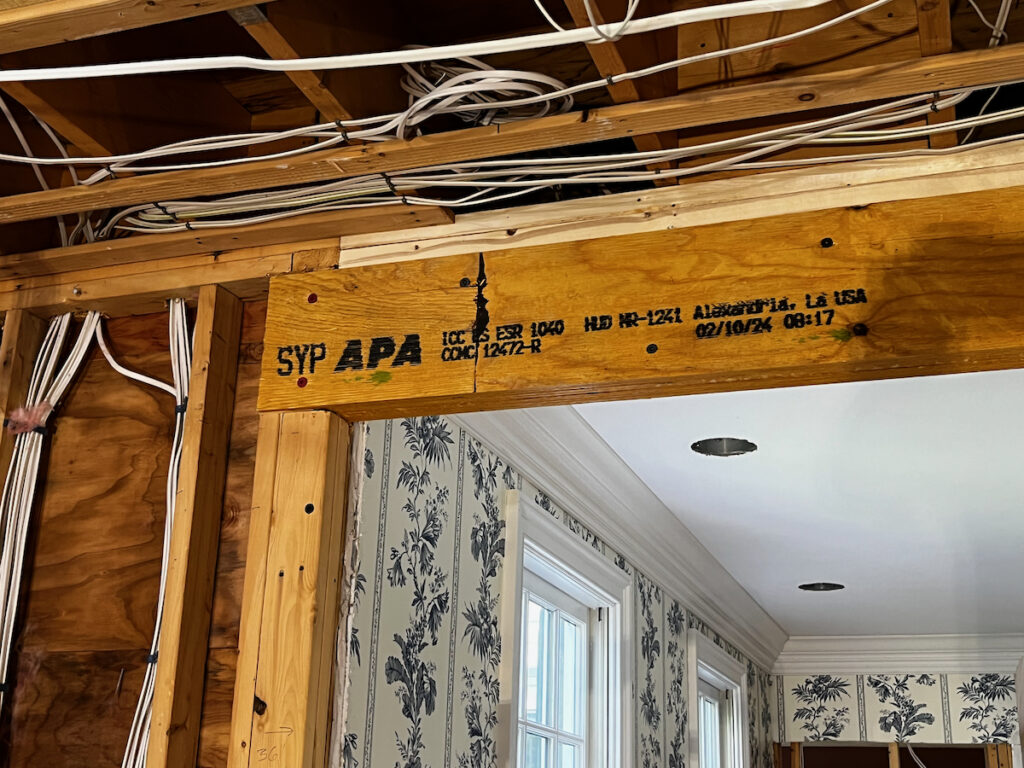
Benefits of LVL Beams
One of the primary advantages of LVL beams is their exceptional strength-to-weight ratio. This means that they can support heavy loads while remaining lightweight, making them easier to handle and install. Additionally, LVL beams are less prone to warping, splitting, or shrinking compared to solid timber, ensuring long-term stability in structural applications.
Another benefit is their sustainability. LVL beams are often made from fast-growing, renewable timber species, making them an environmentally friendly choice. Furthermore, the manufacturing process maximises the use of timber, reducing waste and promoting responsible forestry practices.
Applications of LVL Beams
LVL beams are incredibly versatile and can be used in a variety of applications. They are commonly employed in residential and commercial construction, serving as support beams, floor joists, and roof rafters. Their strength and stability make them ideal for spanning large distances, allowing for open floor plans and expansive interiors.
Moreover, LVL beams can be utilised in specialised applications such as bridge construction and industrial buildings, where high load-bearing capacity is essential. Their adaptability ensures that they can meet the demands of various projects, regardless of size or complexity.
In addition to their structural uses, LVL beams are also favoured in the construction of multi-storey buildings, where they contribute to both the aesthetic and functional aspects of the design. Architects often appreciate the clean lines and uniform appearance of LVL, which can enhance the overall visual appeal of a structure. Furthermore, the ability to fabricate LVL beams in custom sizes allows for innovative design solutions that can accommodate unique architectural requirements, thus pushing the boundaries of modern construction.
Another noteworthy aspect of LVL beams is their performance in terms of fire resistance. While all timber products are subject to fire regulations, LVL beams can be treated to enhance their fire-retardant properties, making them suitable for use in buildings where fire safety is a concern. This treatment can provide additional peace of mind for builders and homeowners, knowing that their structures can withstand potential fire hazards while still maintaining structural integrity.
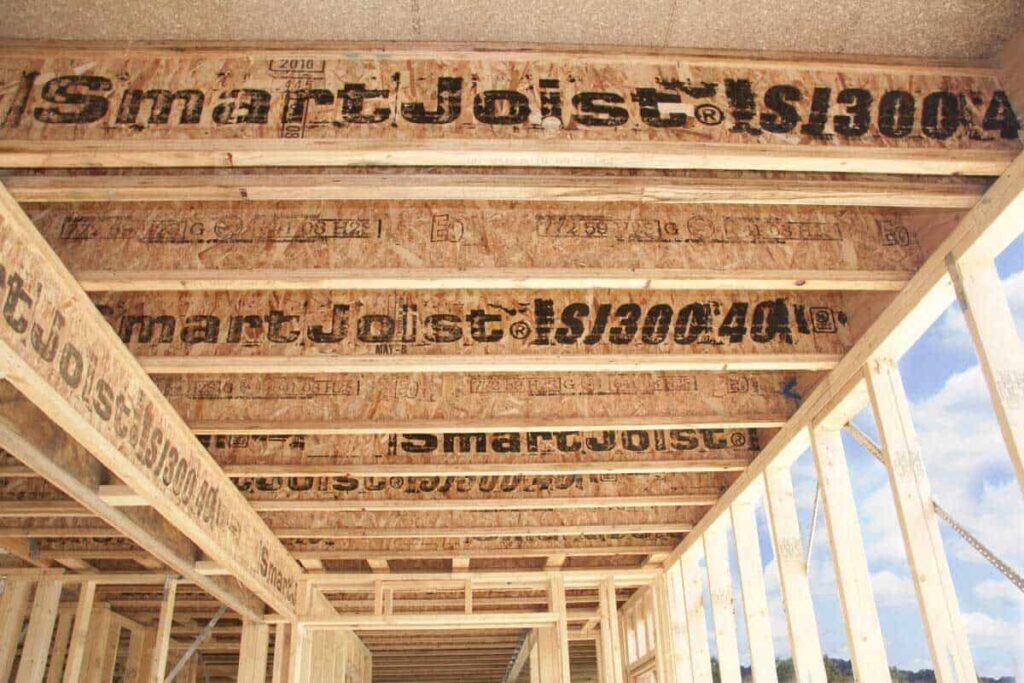
Factors to Consider When Choosing LVL Beams
Selecting the right LVL beam involves considering several factors that can impact the performance and suitability of the material for your specific project. Understanding these factors will help ensure that you make an informed decision.
Load-Bearing Requirements
The first step in choosing an LVL beam is to assess the load-bearing requirements of your project. This includes understanding both the dead load (the weight of the beam itself and any permanent fixtures) and the live load (the weight of occupants, furniture, and other movable items). Consulting with a structural engineer can provide valuable insights into the appropriate load ratings needed for your beams.
Once you have established the load requirements, you can select an LVL beam with the appropriate thickness and depth. Thicker and deeper beams can generally support heavier loads, but they may also require additional support and can be more challenging to install. It’s worth noting that the choice of LVL beam can also influence the overall design aesthetic of your project. A well-chosen beam can complement the architectural style, providing both function and visual appeal, while an ill-suited beam may detract from the overall look of the space.
Span Length
The span length is another critical factor to consider when selecting LVL beams. The span refers to the distance between the supports that the beam will rest on. Longer spans typically require larger or more numerous beams to ensure adequate support. LVL beams are designed to accommodate various span lengths, but it is essential to adhere to the manufacturer’s specifications to avoid structural issues.
When planning your project, consider the layout of your space and how the beams will interact with other structural elements. This will help you determine the optimal span length and configuration for your LVL beams. Additionally, it can be beneficial to explore innovative design solutions, such as open-plan layouts, which can maximise the use of space while still maintaining structural integrity. The careful consideration of span length can also lead to cost savings, as fewer beams may be required, reducing both material and labour costs. Learn more about length on https://sciencedemonstrations.fas.harvard.edu/presentations/length-measurement
Environmental Conditions
Environmental conditions play a significant role in the performance of LVL beams. Factors such as humidity, temperature, and exposure to moisture can affect the integrity and longevity of the material. For instance, in areas with high humidity or frequent rainfall, it may be necessary to choose LVL beams that are treated for moisture resistance.
Additionally, consider the climate in which the structure will be located. In regions prone to extreme temperatures, selecting LVL beams that can withstand thermal expansion and contraction is crucial. Understanding these conditions will help you make a more informed choice and ensure the longevity of your structure. Furthermore, it may be prudent to investigate local building codes and regulations, as these can dictate specific requirements for materials used in construction based on environmental factors. This diligence not only promotes safety but also enhances the durability and performance of your LVL beams in the long run.
Choosing the Right Grade of LVL Beam
LVL beams come in various grades, each designed for specific applications and load requirements. Understanding the differences between these grades is essential for selecting the right beam for your project.
Common LVL Grades
The most common grades of LVL beams include F17, F14, and F11, with F17 being the highest grade. The grade designation indicates the beam’s strength and load-bearing capacity. Higher-grade beams are typically used in applications where greater strength and stability are required, such as in commercial buildings or structures with large open spaces. To learn more about stability click here.
Lower-grade LVL beams, while still strong, may be more suitable for residential applications or areas where the load requirements are less demanding. It is essential to consult with a structural engineer or building professional to determine the appropriate grade for your specific project needs.
Manufacturer Specifications
Each manufacturer may have different specifications for their LVL beams, including dimensions, load ratings, and treatment options. It is crucial to review the manufacturer’s guidelines and ensure that the selected beams meet the necessary building codes and regulations.
Additionally, consider the reputation and reliability of the manufacturer. Choosing a reputable brand ensures that you are receiving a quality product that has been tested and certified for safety and performance.
Installation Considerations
Proper installation of LVL beams is vital for ensuring their performance and longevity. Understanding the installation process can help prevent issues down the line and ensure that your structure remains safe and stable.
Support and Bracing
When installing LVL beams, it is essential to provide adequate support and bracing. This includes ensuring that the beams are properly anchored to the supporting walls or columns and that they are level. Failure to provide proper support can lead to sagging or structural failure over time.
Bracing is also crucial, particularly for longer spans. Diagonal bracing can help prevent lateral movement and provide additional stability, especially in areas prone to high winds or seismic activity. Consulting with a structural engineer can provide guidance on the best bracing techniques for your specific installation.
Tools and Equipment
Using the right tools and equipment is essential for a successful installation. Ensure that you have access to appropriate lifting equipment, such as cranes or hoists, to safely manoeuvre the LVL beams into place. Additionally, using proper fastening techniques, such as screws or bolts, will help secure the beams and maintain their structural integrity.
It is also advisable to have a qualified contractor or builder oversee the installation process. Their expertise can help ensure that the beams are installed correctly and in compliance with local building codes.
Maintenance and Inspection
Once your LVL beams are installed, regular maintenance and inspection are crucial for ensuring their long-term performance. This involves monitoring for signs of wear, damage, or moisture intrusion that could compromise the structural integrity of the beams.
Regular Inspections
Conducting regular inspections of your LVL beams can help identify potential issues before they become significant problems. Look for signs of sagging, cracking, or warping, as well as any signs of pest infestation or moisture damage. Addressing these issues promptly can help extend the lifespan of your beams and maintain the safety of your structure.
Maintenance Practices
Maintaining a dry environment around your LVL beams is essential for preventing moisture-related issues. Ensure that gutters and downspouts are functioning correctly to divert water away from the structure. Additionally, consider using dehumidifiers in areas prone to high humidity to help protect the beams from moisture damage.
In the event of any damage, consult with a professional to assess the situation and determine the best course of action. In some cases, it may be possible to repair the beams, while in others, replacement may be necessary.
Conclusion
Choosing the right LVL beam for your structural needs is a critical decision that can impact the safety, stability, and longevity of your project. By understanding the benefits of LVL beams, considering key factors such as load requirements and environmental conditions, and selecting the appropriate grade and manufacturer, you can ensure that your construction or renovation project is successful.
Additionally, proper installation and ongoing maintenance are essential for maximising the performance of your LVL beams. By following these guidelines and consulting with professionals when necessary, you can confidently choose the right LVL beam for your needs and create a safe, durable structure that stands the test of time.